Who Else Wants Info About What Are The Common Motor Controllers

Automatic Sequential Motor Control Circuit Power &
Decoding the Mystery
1. A Quick Layman's Explanation
Ever wonder how that electric scooter knows exactly how much oomph to give you when you twist the throttle? Or how your washing machine spins clothes at precisely the right speed for delicates versus heavy towels? The unsung hero behind these marvels of modern convenience is the motor controller. Think of it as the brain that directs the muscles (the motor, in this case). It takes your instructions — whether it's a speed setting, a direction change, or a full stop — and translates them into electrical signals that tell the motor what to do.
Basically, without a motor controller, your motor would either be stuck at full blast or completely inert. Not exactly ideal for nuanced control, right? It's like having a car with only two settings: pedal to the metal or parked. A good motor controller provides smooth, efficient, and safe operation, protecting both the motor and the connected equipment from damage. So, the next time you effortlessly adjust the speed of your ceiling fan, give a silent nod of appreciation to the tiny but mighty motor controller.
Motor controllers manage the speed, torque, direction, and even braking of electric motors. They act as intermediaries between the power source and the motor, ensuring the motor receives the correct voltage and current to perform its assigned task. This also helps prevent overloads, short circuits, and other electrical mishaps that could fry your motor (and potentially more).
They're used everywhere! From the industrial robots building your car to the electric vehicle you might drive, motor controllers are integral to countless applications. They're found in household appliances, HVAC systems, power tools, and pretty much anything that uses an electric motor and needs more finesse than simply "on" and "off". Think of them as the conductors of the motor orchestra, ensuring that everything plays in harmony.

The Most Common Motor Controller Wiring Diagrams And Programming
The Usual Suspects
2. A Rundown of Popular Options
Now that we know what motor controllers do, let's look at some common types. There's not a one-size-fits-all solution; the best type depends on the specific motor, application, and performance requirements. Its like choosing the right spice for a dish — get it wrong, and things just wont taste right (or, in this case, things just won't work right).
First up, we have On/Off (or Across-the-Line) Starters. These are the simplest type, directly connecting the motor to the power supply. They're like the light switch for your motor: either fully on or completely off. Theyre fine for applications where a sudden start and full speed are acceptable, but they arent great for delicate operations or situations where you need to avoid a jolt to the system.
Then there are Reduced Voltage Starters. These clever devices limit the inrush current when the motor starts. Think of it as easing the motor into action instead of throwing it into the deep end. This reduces stress on the motor and the electrical grid, making them ideal for larger motors or systems sensitive to voltage fluctuations. Types include autotransformer, part winding, and resistor starters, each with its own method of reducing the initial voltage.
Variable Frequency Drives (VFDs), also known as adjustable speed drives (ASDs), are the rock stars of motor control. They allow you to precisely control the motor speed by adjusting the frequency of the power supply. Imagine having a volume knob for your motor! VFDs are super versatile and can save energy by only using the power needed for the task at hand. They're used in everything from conveyor belts to pump systems to give very fine-tuned control.
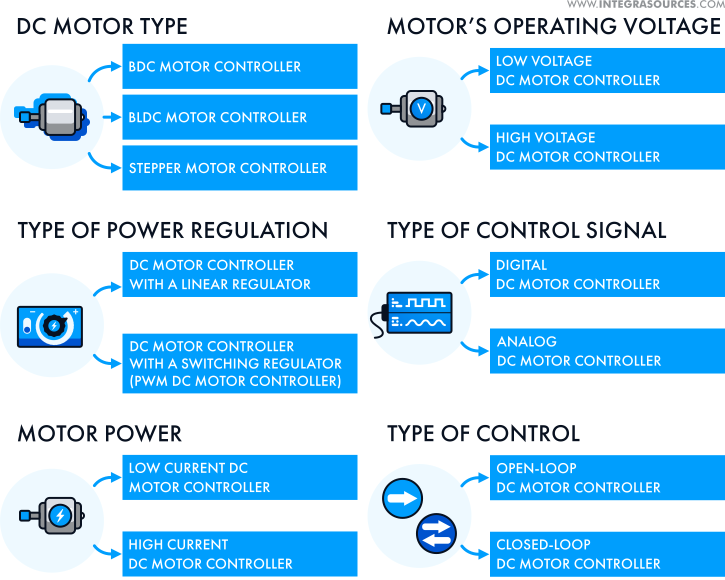
Construction And Working Principle Of Bldc Motor Using Pwm
Under the Hood
3. A Peek Inside the Black Box
Alright, time to dive a little deeper, but I promise to keep the jargon to a minimum. At their core, motor controllers use electronic components like transistors, diodes, and microcontrollers to regulate the flow of electricity to the motor. It's like a sophisticated plumbing system for electrons, directing them where they need to go and when.
For example, a VFD takes the incoming AC power, converts it to DC, and then inverts it back to AC at a different frequency. By changing the frequency, the VFD can precisely control the motor speed. The microcontroller acts as the brain, processing inputs from sensors and user commands to adjust the output voltage and frequency accordingly.
Sophisticated motor controllers often incorporate feedback loops. This means they monitor the motor's performance — speed, torque, current — and adjust the control signals to maintain the desired operation. Think of it like cruise control in your car: it constantly monitors your speed and adjusts the engine power to keep you at the set speed, even when going uphill or downhill.
Modern motor controllers are often programmable, allowing you to customize their behavior to suit specific applications. You can set parameters like acceleration rates, deceleration rates, torque limits, and fault conditions. This flexibility makes them adaptable to a wide range of tasks and allows you to optimize performance and protect the motor from damage. It's like having a custom-tailored suit for your motor, ensuring a perfect fit and optimal performance.
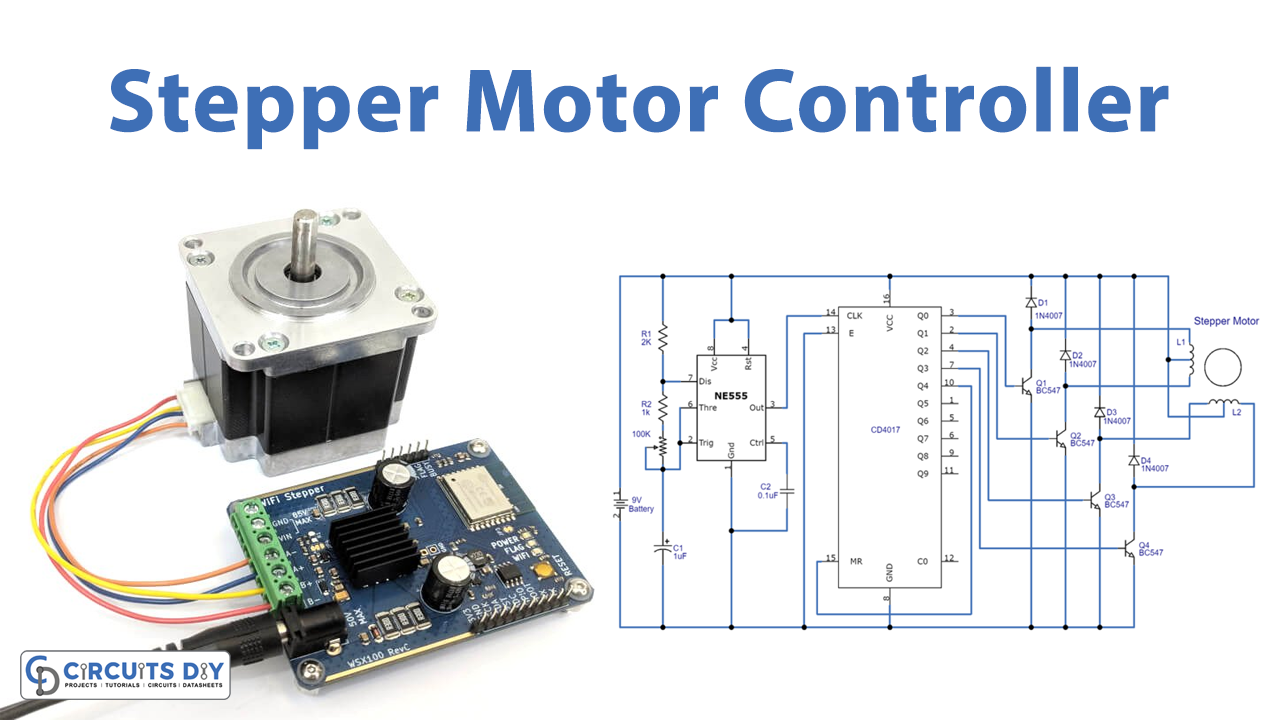
Servo Motor Driver Circuit
Choosing the Right Controller
4. Making the Smart Choice
Selecting the right motor controller is crucial for optimal performance, energy efficiency, and motor longevity. But with so many options available, how do you choose the best one for your application? Dont worry, its not as daunting as it seems. Let's break down some key factors to consider.
First and foremost, motor type matters. Different motors (AC induction, DC, servo, stepper, etc.) require different types of controllers. Make sure the controller is compatible with your motor's voltage, current, and control requirements. Its like trying to put the wrong fuel in your car; it just won't run (and might even cause damage).
Next, consider the application requirements. What kind of control do you need? Do you need precise speed control, torque control, or just simple on/off switching? Do you need to limit inrush current to avoid voltage dips? The answers to these questions will help narrow down your options. Think about the specific demands of the job and choose a controller that can handle them efficiently and reliably.
Finally, don't forget about safety features. Look for controllers with built-in protection against overloads, short circuits, overvoltage, and undervoltage. These features can prevent costly damage to the motor and connected equipment, and they can also help ensure the safety of personnel. It's like having an insurance policy for your motor, protecting it from unforeseen events.
Also, consider cost and size as it can effect your decision on the best controller. Often, a smaller device might be less costly, but also may not have all of the required needs. Size is crucial because it can limit the controllers placement.
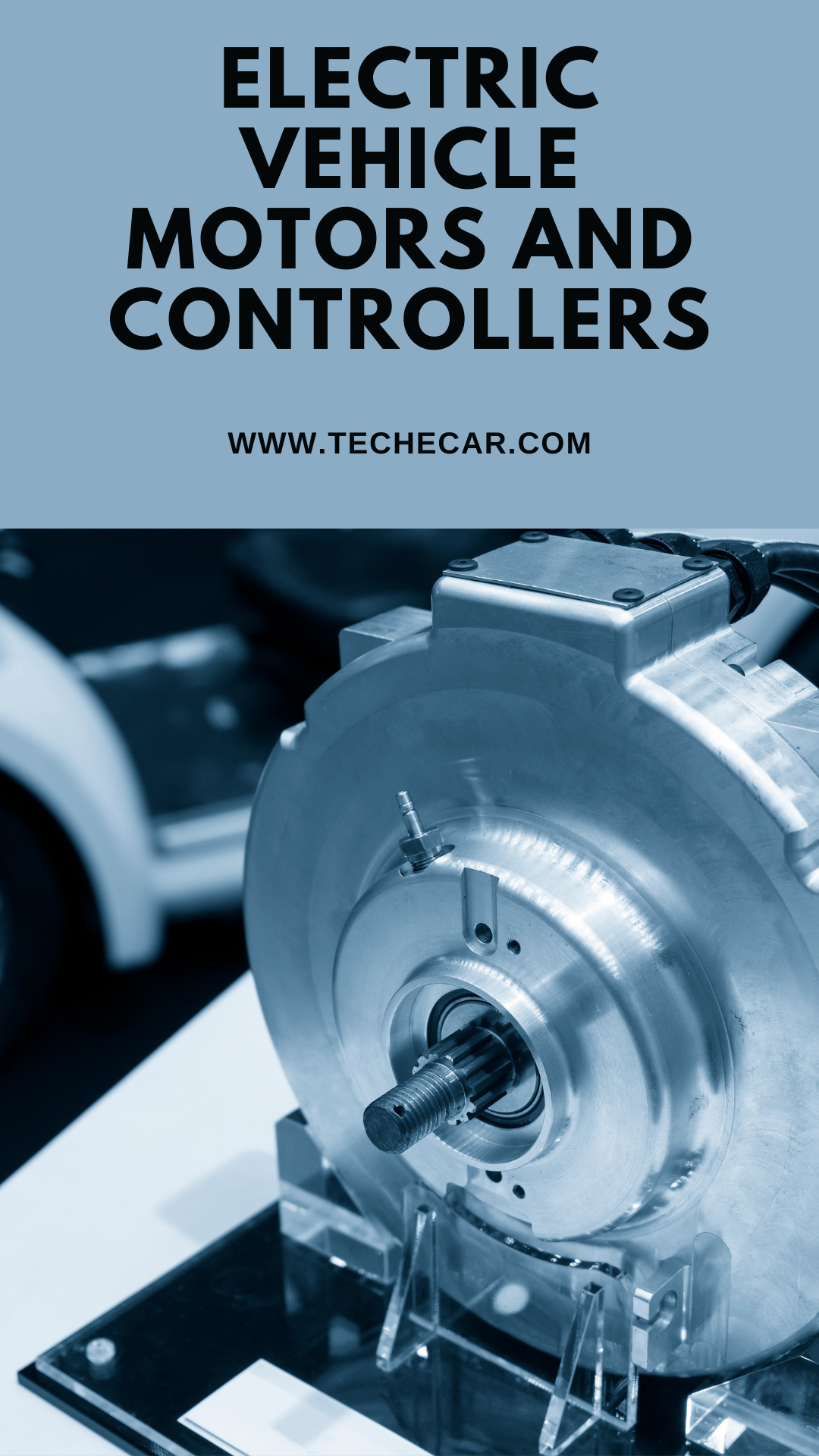
Future Trends
5. Gazing into the Crystal Ball
The world of motor control is constantly evolving, driven by advancements in technology and the growing demand for greater efficiency and performance. So, what does the future hold? Expect to see even more sophisticated and intelligent motor controllers in the years to come.
One major trend is the increasing integration of smart features and connectivity. Motor controllers are becoming more like miniature computers, with built-in sensors, data logging capabilities, and communication interfaces. This allows for remote monitoring, diagnostics, and control, enabling predictive maintenance and optimized performance.
Artificial intelligence (AI) and machine learning (ML) are also starting to play a role. AI-powered motor controllers can learn from past performance and automatically adjust their settings to optimize energy efficiency and extend motor life. Imagine a motor controller that can anticipate potential problems and take corrective action before they occur!
Finally, expect to see continued improvements in power electronics and materials. New semiconductor technologies like silicon carbide (SiC) and gallium nitride (GaN) are enabling smaller, more efficient, and more robust motor controllers. These advancements are paving the way for higher power densities and improved performance in demanding applications like electric vehicles and industrial automation. The future of motor control is looking bright!

Simple BLDC Motor Controller Circuit Using Irfz44n Mosfet YouTube
FAQ
6. Quick Answers to Common Queries
Let's tackle some frequently asked questions to solidify your understanding.
Q: What's the difference between a motor starter and a motor controller?
A: Think of a motor starter as a basic type of motor controller. A starter primarily provides on/off control, while a motor controller can offer more sophisticated features like speed control, torque limiting, and protection features.
Q: Can I use any motor controller with any motor?
A: Absolutely not! Compatibility is key. You need to match the controller's voltage, current, and control requirements with the motor's specifications. Using an incompatible controller can damage the motor or the controller itself.
Q: How can a VFD save energy?
A: VFDs save energy by allowing the motor to operate at the precise speed needed for the task. Instead of running at full speed all the time and wasting energy, the VFD adjusts the motor speed to match the load, reducing energy consumption.